Crazing in ceramics is a common issue that can detract from the aesthetic and structural integrity of finished pieces. It manifests as a network of fine cracks on the surface of glazed ceramics, often caused by a mismatch between the expansion and contraction rates of the clay body and the glaze during the firing and cooling processes. Understanding the factors that contribute to crazing is essential for ceramic artists and potters aiming to create durable and visually appealing work. This guide will explore effective techniques on how to avoid crazing in ceramics, ensuring that your ceramics maintain their beauty and functionality over time.
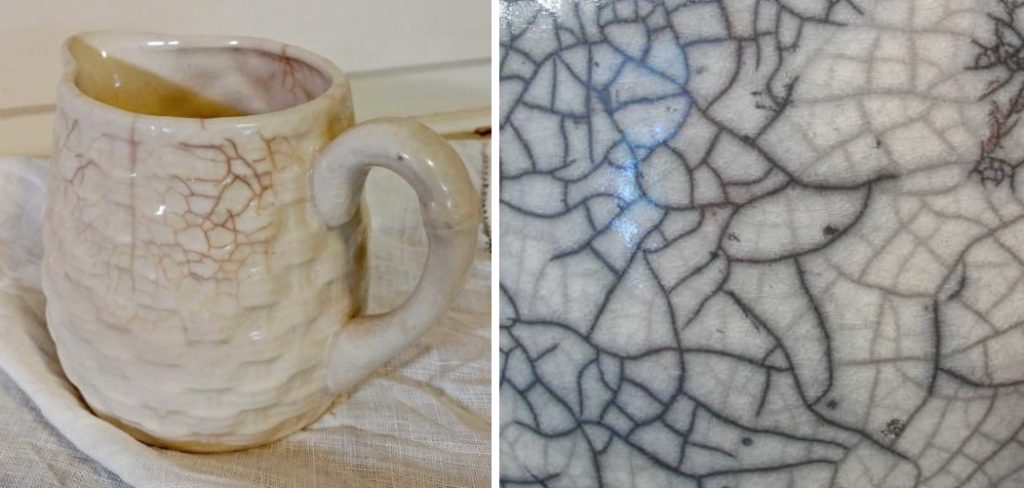
Understanding Crazing
Crazing occurs when the glaze of a ceramic piece expands and contracts at a different rate than the underlying clay body. This discrepancy can result from various factors, including the choice of materials, firing temperature, and cooling rates. When the glaze cools more quickly than the clay, tension builds up, leading to the formation of surface cracks.
Additionally, environmental conditions and the thickness of the glaze can exacerbate this issue. By gaining a deeper understanding of how these elements interact, ceramic artists can make informed decisions regarding material selection and firing techniques, ultimately reducing the risk of crazing and enhancing the longevity of their work.
Types of Ceramics Affected
Crazing can affect various types of ceramics, each with its unique properties and characteristics. Porcelain, known for its delicate and translucent qualities, is particularly vulnerable due to its high firing temperatures and fine glaze. Stoneware, while generally more durable, can also suffer from crazing if the glaze and clay body are not well-matched. Earthenware, which is often fired at lower temperatures, may exhibit crazing as a result of thicker glaze applications or rapid cooling.
Additionally, decorative ceramics, which are often subjected to different environmental conditions and usage, can show signs of crazing if they are not properly formulated or fired. Recognizing which types of ceramics are most susceptible to this issue is crucial for artists in planning their work and ensuring long-lasting results.
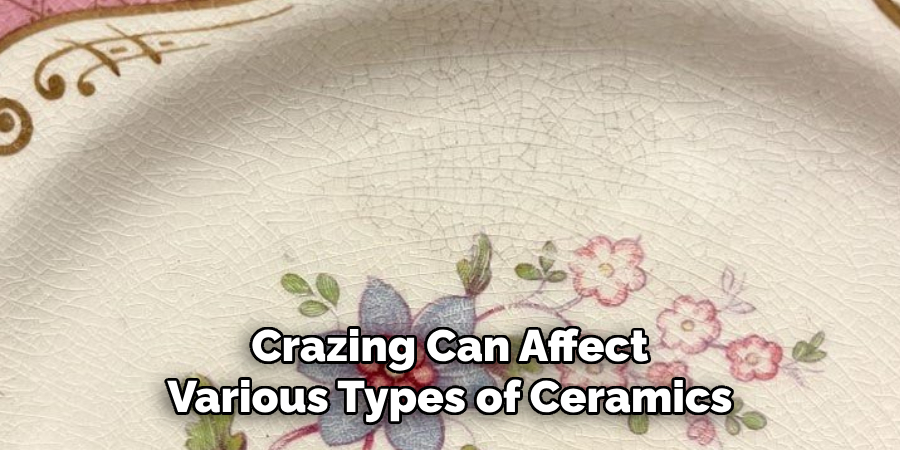
10 Methods How to Avoid Crazing in Ceramics
1. Selecting the Right Clay Body
The choice of clay body plays a crucial role in preventing crazing. Different clay bodies have varying thermal expansion properties, which can affect how they respond to temperature changes during firing. To minimize the risk of crazing, select a clay body with a thermal expansion coefficient that matches or is compatible with your glaze. For instance, stoneware and porcelain clays typically have lower thermal expansion rates and are less prone to crazing when paired with appropriate glazes. Consulting with your clay supplier or testing different clay bodies can help you find the most suitable option for your ceramic projects.
2. Choosing Compatible Glazes
Glaze compatibility is essential for preventing crazing. Each glaze has a specific coefficient of expansion, and it must be compatible with the clay body and other glazes used. When a glaze’s expansion rate significantly differs from that of the clay body, it can lead to stress and cracking. To avoid this, conduct glaze tests by applying the glaze to small test pieces and firing them to observe any potential crazing. Ensure that your glazes are formulated to match the thermal expansion characteristics of your chosen clay body, and avoid mixing glazes with vastly different expansion rates.
3. Controlling the Firing Temperature
Proper temperature control during firing is crucial for preventing crazing. Both under-firing and over-firing can cause issues with glaze and clay expansion. To achieve optimal results, use a reliable kiln with accurate temperature control and calibration. Gradually increase the temperature to allow the clay and glaze to expand and contract uniformly. Avoid rapid temperature changes, as they can induce stress and lead to crazing.
4. Ensuring Even Glaze Application
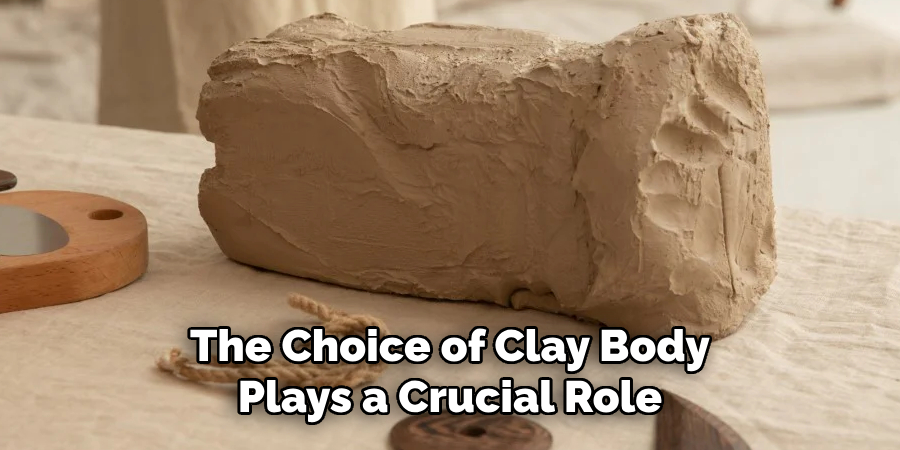
Uneven glaze application can contribute to crazing by creating areas of varying thickness and stress. To achieve a consistent glaze layer, apply the glaze evenly using appropriate techniques, such as dipping, brushing, or spraying. Pay attention to the thickness of the glaze; too thick a layer can lead to excessive stress during firing, while too thin a layer might result in incomplete coverage. Regularly inspect and practice your glazing techniques to ensure uniform application, and test different methods to find the most effective approach for your ceramics.
5. Using a Well-Formulated Glaze Recipe
The formulation of your glaze recipe can significantly impact the likelihood of crazing. Ensure that your glaze recipe includes the appropriate balance of ingredients, such as fluxes, silica, and alumina, to achieve a stable and durable glaze. Experiment with different glaze recipes and adjust the proportions of ingredients to find a formula that minimizes crazing. Consider using commercial glazes with proven stability or consult glaze formulation guides to create a balanced recipe.
6. Allowing Adequate Drying Time
Proper drying of ceramics before firing is essential to prevent crazing. Inadequate drying can result in trapped moisture within the ceramic body, leading to cracking and crazing during firing. Allow your ceramic pieces to dry slowly and thoroughly in a well-ventilated area. Avoid exposing them to rapid temperature changes or direct sunlight, as this can cause uneven drying and stress. Use a drying rack or place the pieces on a flat surface to ensure even air circulation. Patience and careful drying practices will help prevent issues related to moisture and reduce the risk of crazing.
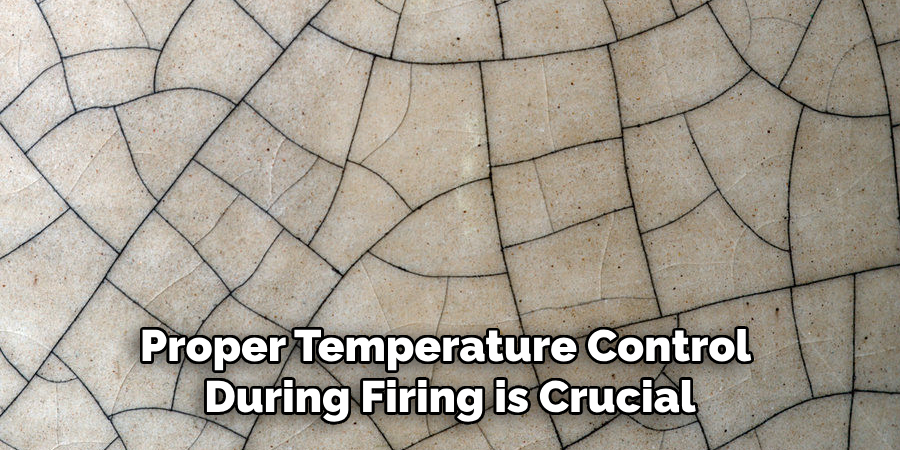
7. Maintaining Kiln Atmosphere
The kiln atmosphere during firing can influence the development of crazing. An oxidizing or reducing atmosphere can affect how the glaze and clay body interact. For most ceramics, an oxidizing atmosphere (where there is ample oxygen) is preferred to achieve a stable glaze finish. Ensure that your kiln is properly ventilated and that the firing environment is consistent. Avoid introducing contaminants or materials that can affect the kiln’s atmosphere.
8. Avoiding Thermal Shock
Thermal shock occurs when ceramics experience rapid temperature changes, causing stress and potential crazing. To prevent thermal shock, gradually heat and cool your kiln and ceramic pieces. Avoid placing cold ceramics into a hot kiln or exposing hot ceramics to cold air. Implement a controlled ramp-up and cool-down period in your firing schedule to allow the ceramics to adjust to temperature changes gradually.
9. Properly Preparing Ceramic Surfaces
Surface preparation before glazing can impact the likelihood of crazing. Ensure that ceramic surfaces are clean and free of dust, oils, or other contaminants that can interfere with glaze adhesion and bonding. Use a damp sponge or cloth to wipe the surfaces before applying the glaze. Additionally, check for any surface defects or imperfections that could contribute to uneven glaze application. Proper surface preparation will help ensure a smooth and even glaze layer, reducing the risk of crazing.
10. Testing and Monitoring
Regular testing and monitoring of your ceramics, clay bodies, and glazes are essential for identifying potential issues and making necessary adjustments. Create test tiles or sample pieces to experiment with different materials and techniques. Observe the results and make notes on any signs of crazing or other issues. Regularly review and update your firing schedules, glaze formulations, and handling practices based on your observations. Continuous testing and monitoring will help you refine your processes and reduce the likelihood of crazing in your ceramic pieces.
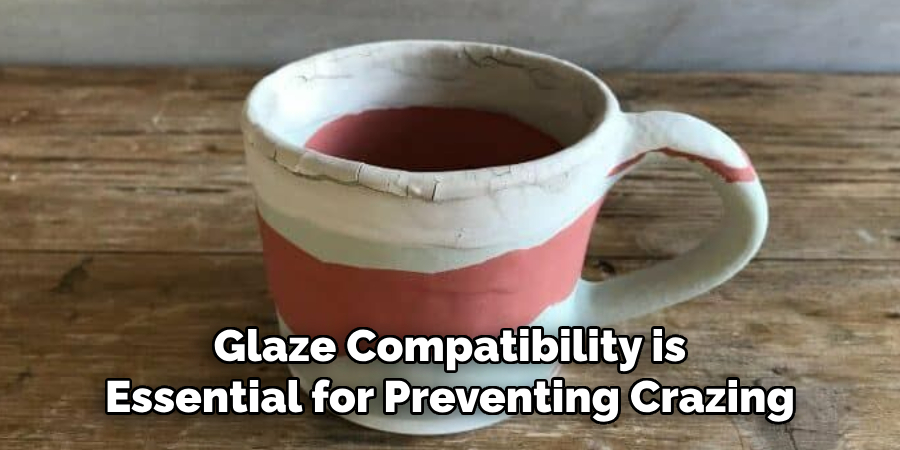
Common Mistakes to Avoid
1. Rushing the Drying Process
One of the most common mistakes is to rush the drying process of ceramic pieces. Skipping adequate drying time can lead to trapped moisture, resulting in cracking or crazing during firing. Always prioritize slow and thorough drying to ensure the best results.
2. Neglecting Surface Preparation
Failing to properly clean and prepare ceramic surfaces before glazing can significantly impact glaze adhesion. Many artists overlook this step, leading to uneven application and increased chances of crazing. Always ensure surfaces are free of dust and contaminants for optimal glaze bonding.
3. Using Incompatible Materials
Choosing clay bodies and glazes that are not compatible can be detrimental to the final product. Using materials with vastly different thermal expansion rates may cause stress and crazing. It’s important to research and test combinations to find compatible pairs for your projects.
4. Ignoring Firing Schedules
Every ceramic piece is unique, and using a one-size-fits-all firing schedule can work against you. Ignoring specific clay and glaze requirements can lead to issues like crazing. Be sure to adapt your firing schedules based on the materials you are using for consistent results.
5. Overlooking Kiln Maintenance
A poorly maintained kiln can lead to uneven heating and unpredictable atmospheres. Regular kiln maintenance, including checking for leaks and ensuring consistent temperature, is essential to prevent crazing and other firing issues. Always ensure your kiln is in good working order before each firing.
Conclusion
In conclusion, understanding and addressing the factors that contribute to crazing in ceramics is essential for achieving high-quality, durable pieces. By controlling the firing temperature, ensuring even glaze application, using well-formulated glaze recipes, and allowing adequate drying time, ceramists can significantly reduce the risk of crazing. Thanks for reading, and we hope this has given you some inspiration on how to avoid crazing in ceramics!
With a keen eye for detail and a deep understanding of the firing process, I bring ceramics to life as a skilled kiln operator. My expertise ensures that each piece reaches its full potential, achieving the perfect balance of strength and beauty. I take pride in overseeing the critical final stage of pottery creation, transforming raw clay into stunning, durable art. 🎨
From monitoring temperatures to perfecting firing schedules, I ensure that every piece is fired to perfection. My role is not just about operating the kiln; it’s about understanding the unique needs of each creation and bringing out its best qualities.
Join me on this journey of precision and passion, where every firing tells a story. Whether it’s a delicate vase or a robust sculpture, I am dedicated to making sure that every piece that comes out of the kiln is a masterpiece. 🏺✨
Toby Rede is a professional potter focused on creating functional and artistic ceramics. His work blends natural textures with modern forms, often inspired by sustainable gardening and outdoor environments. Toby’s pottery emphasizes both utility and beauty, reflecting his philosophy of intentional craftsmanship. On the blog, he shares insights on integrating handmade objects into everyday life.
Education
- Master of Fine Arts in Ceramics, California College of the Arts
Professional Focus
- Creating practical pottery for everyday use.
- Using unique styles and techniques to convey narratives in ceramics.
Professional Accomplishments
- Showcased work in local and national art galleries, gaining recognition for craftsmanship.
- Received accolades for innovative designs in pottery competitions.