Firing ceramics in a microwave is an innovative technique that allows artists and hobbyists to complete the firing process quickly and with greater energy efficiency than traditional kiln firing. This method uses a specialized device called a microwave kiln, enabling the transformation of clay or glaze materials to their finished, hardened state by utilizing microwave energy. Ideal for small projects or those working within limited spaces, microwave firing offers a convenient and accessible way to explore the art of ceramics without the need for large, industrial equipment. In this guide, we’ll explore how to fire ceramics in microwave, ensuring beautiful and long-lasting results.
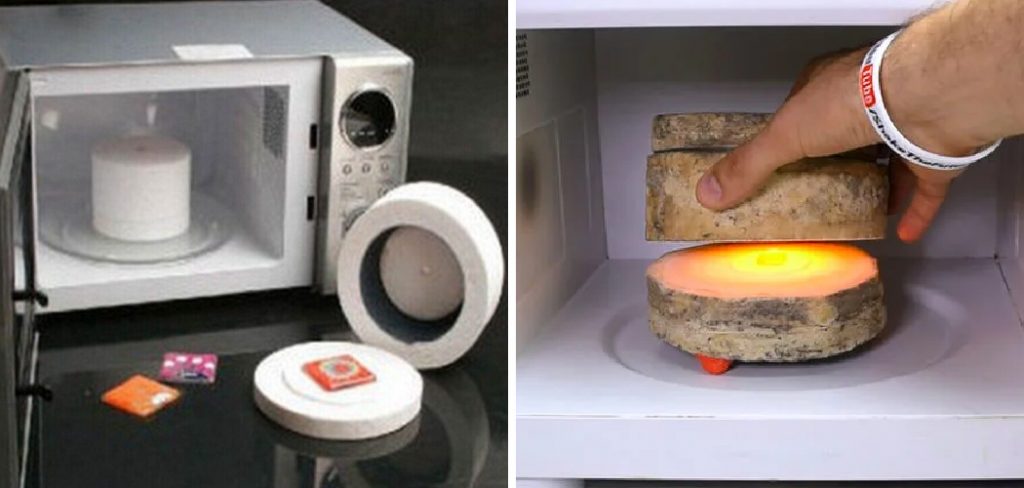
What is a Microwave Kiln and How It Works
A microwave kiln is a compact, specialized device designed to fit inside a standard microwave oven, allowing for the firing of ceramics using microwave energy. The kiln is typically composed of a fiber-based insulating shell that contains a silicon carbide lining, which absorbs the microwave radiation and converts it into heat. When placed in a microwave oven, the silicon carbide becomes red-hot, reaching temperatures necessary to harden and vitrify clay or glaze materials. The heat generated inside the kiln is sufficient to fire small ceramic pieces efficiently,
making this method particularly suitable for small batch processes, jewelry making, and experimental projects. The advantage of using a microwave kiln lies in its ability to achieve the desired temperatures rapidly, often within minutes, and with reduced energy consumption, making it an eco-friendly alternative to traditional firing methods.
Types of Ceramics and Clay That Can Be Fired Safely in a Microwave Kiln
When using a microwave kiln, it’s important to select appropriate types of ceramics and clay to ensure successful and safe firing. Low-fire clays, such as earthenware, are ideally suited for microwave kiln firing due to their relatively low maturation temperatures, which align with the capabilities of most microwave kilns. These clays can beautifully transform into finished pieces with a glossy or matte appearance, depending on the chosen glaze. Additionally, certain types of small ceramic jewelry, beads, and decorative items made from compatible low-fire materials can also be fired effectively.
It’s crucial to avoid high-fire clays or large items that require higher temperatures and longer firing times, as these exceed the safe operating parameters of a microwave kiln and could potentially cause damage to the equipment or uneven results. Always consult the manufacturer’s guidelines to ensure the materials being used are suitable for microwave kiln firing.
Materials Needed for Firing Ceramics in a Microwave
To successfully fire ceramics using a microwave kiln, you need to prepare and gather the appropriate materials and tools. Here is a list of essentials:
- Microwave Kiln: The primary tool, a microwave kiln is specifically designed to work within a standard household microwave. Ensure it fits properly with some space for airflow.
- Microwave Oven: A standard microwave, ideally one that you dedicate solely to firing, as it may not be safe for food use afterward.
- Low-Fire Clay or Ceramic Materials: Suitable clays include earthenware that matures at lower temperatures, as well as prepared ceramic bisques ideal for glazing and refiring.
- Glazes and Decorating Materials: Choose appropriate low-fire glazes or underglazes compatible with microwave kiln temperatures to finish your pieces.
- Heat-Resistant Gloves: To handle the kiln safely during and after the firing process, preventing burns from high temperatures.
- Kiln Stilts: These can be used to elevate ceramics pieces within the kiln, ensuring they don’t stick to the kiln base during firing.
- Protective Surface: A heat-safe surface or ceramic fiber mat to place the kiln on, both during and after firing to protect countertops.
- Tongs: For safely handling hot items, especially when removing the kiln lid or repositioning ceramics inside.
Having these materials at hand will ensure a smooth firing process, allowing you to focus on crafting beautiful ceramic pieces.
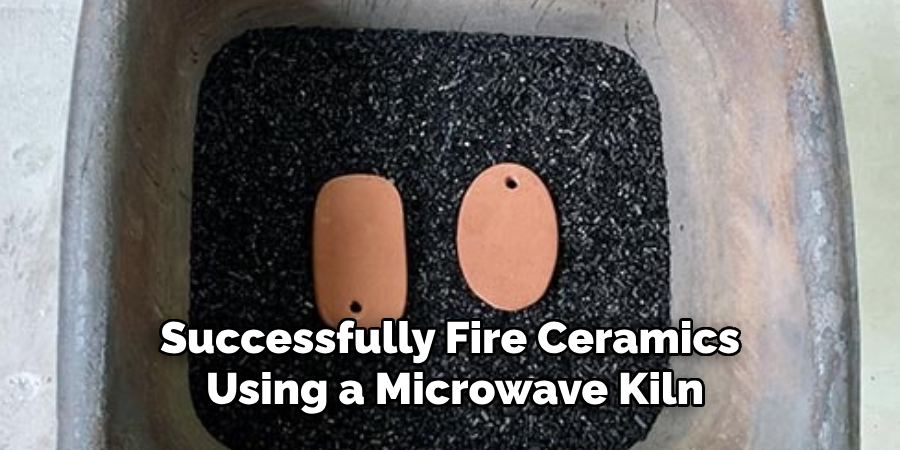
10 Methods How to Fire Ceramics in Microwave
For DIY enthusiasts, pottery beginners, and ceramic artists, microwave firing can transform your crafting process. It’s quicker, more efficient, and perfect for small-scale projects. Explore these 10 methods to fire ceramics using your microwave and unlock new possibilities in your creative endeavors.
1. Understanding Microwave Safe Clay
Start by choosing the right clay. Not all are suitable for microwave firing. Look for microwave-safe clays specifically designed for this purpose. They often contain materials like aluminum trihydrate, which aids in even heating without damaging the clay or the microwave.
2. Using a Microwave Kiln
A microwave kiln is a small ceramic vessel lined with a fiber blanket. Place your ceramic piece inside, and the kiln will concentrate microwave energy to reach the required temperature for firing. This method is ideal for small projects and offers a convenient alternative to traditional kilns.
3. Preparing Your Workspace
Ensure your workspace is safe and organized. Keep your microwave clean and free of food particles. Use heat-resistant gloves when handling hot items, and ensure there is adequate ventilation to avoid inhaling fumes released during firing.
4. Monitoring Firing Times
Timing is crucial in microwave firing. Start with shorter intervals, around 5 minutes, and gradually increase as needed. Monitor your pieces closely to prevent over-firing, which can lead to cracks or breakage. Always refer to clay manufacturer guidelines for specific timing recommendations.
5. Using Proper Supports
To prevent sagging or warping during firing, support your ceramic pieces appropriately. Utilize microwave-safe supports, like kiln stilts or stands, to maintain the shape and structure of your creations.
6. Testing for Even Heating
Even heating is key to successful microwave firing. Before placing your actual piece inside, do a test run with a similar size and shape. Adjust the placement and microwave settings until you achieve uniform heating throughout the piece.
7. Experimenting with Glazes
Glazing in a microwave requires specific glazes designed for low-temperature firing. Apply a thin, even coat and ensure it’s completely dry before firing. Experiment with different colors and finishes to achieve your desired look.
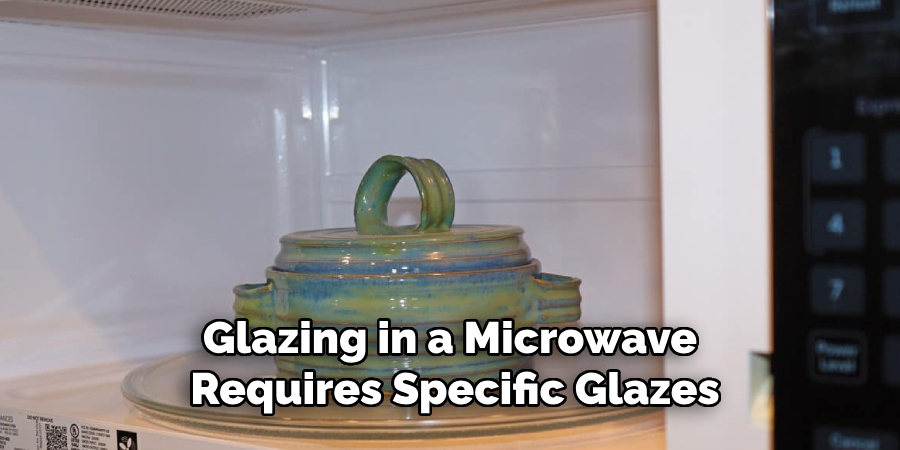
8. Cooling Down Safely
Post-firing, allow your ceramics to cool slowly inside the microwave kiln. Abrupt temperature changes can cause cracking. Once cool to the touch, carefully remove your pieces, using protective gloves.
9. Troubleshooting Common Issues
Cracks, bubbles, or uneven surfaces can occur if firing conditions aren’t optimal. If you encounter these issues, revisit your clay choice, firing times, or glaze application. Make incremental adjustments to find the right balance.
10. Documenting Your Process
Keep a journal of your microwave firing adventures. Record details about clay types, firing times, and results. Over time, this data will help refine your techniques and create consistently stunning ceramics.
Things to Consider When Firing Ceramics in a Microwave
When embarking on the journey of firing ceramics in a microwave, certain considerations are vital to ensure both safety and success. Firstly, always prioritize using a dedicated microwave for firing. This is because the kiln may release harmful substances, making the microwave unsuitable for food use afterward. Secondly, recognize that size limitations apply; only small pieces should be fired to ensure even heating and prevent damage to both the ceramics and the microwave. Additionally, consistently adhere to manufacturer guidelines for the microwave kiln, clays, and glazes to avoid exceeding temperature limits that may lead to breakage or mishaps.

Finally, maintain a vigilant approach to monitoring the firing process, paying close attention to any unusual odors or smoke, which might indicate improper conditions. Taking these factors into account will enhance both the safety and quality of your ceramic creations.
Common Mistakes to Avoid
When firing ceramics in a microwave, certain mistakes can derail your project or even cause damage to your equipment. One common issue is using unsuitable clays or glazes. Always ensure that both your clay and glazes are labeled as microwave-safe and compatible with low-temperature firing. Another mistake is overloading the microwave kiln: firing too many pieces at once can lead to uneven heating and cracking. Additionally, failing to properly dry your pieces before firing can result in steam-related explosions inside the kiln.
Avoid heating pieces too quickly, as this can cause thermal shock and breakage; instead, gradually increase firing times to reach the desired temperature. Lastly, neglecting to monitor the entire firing process, including cooling, can lead to unanticipated problems. Being attentive and adhering to recommended guidelines will help you achieve successful microwave-fired ceramics.
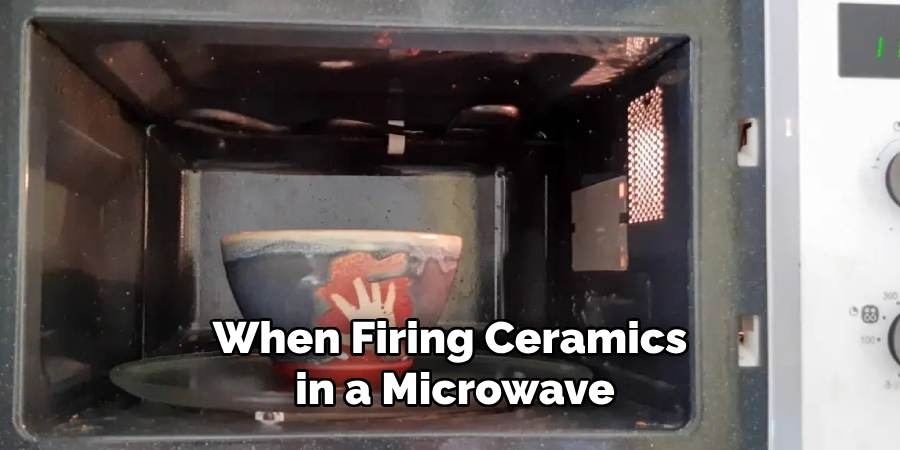
Conclusion
Incorporating microwave firing into your ceramic crafting can be a transformative experience, offering a flexible and efficient approach that suits a variety of creative projects. By adhering to guidelines around clay and glaze selection, as well as proper firing techniques, you can achieve remarkable results while maintaining safety. Embrace the learning curve with patience, and be open to experimentation and adjustments. Over time, you will refine your skills, leading to personal satisfaction and artistic expression.
Ultimately, the marriage of ancient ceramic art with modern technology opens new avenues for innovation and creativity in the world of ceramics. Thanks for reading, and we hope this has given you some inspiration on how to fire ceramics in microwave!
With a keen eye for detail and a deep understanding of the firing process, I bring ceramics to life as a skilled kiln operator. My expertise ensures that each piece reaches its full potential, achieving the perfect balance of strength and beauty. I take pride in overseeing the critical final stage of pottery creation, transforming raw clay into stunning, durable art. 🎨
From monitoring temperatures to perfecting firing schedules, I ensure that every piece is fired to perfection. My role is not just about operating the kiln; it’s about understanding the unique needs of each creation and bringing out its best qualities.
Join me on this journey of precision and passion, where every firing tells a story. Whether it’s a delicate vase or a robust sculpture, I am dedicated to making sure that every piece that comes out of the kiln is a masterpiece. 🏺✨
Toby Rede is a professional potter focused on creating functional and artistic ceramics. His work blends natural textures with modern forms, often inspired by sustainable gardening and outdoor environments. Toby’s pottery emphasizes both utility and beauty, reflecting his philosophy of intentional craftsmanship. On the blog, he shares insights on integrating handmade objects into everyday life.
Education
- Master of Fine Arts in Ceramics, California College of the Arts
Professional Focus
- Creating practical pottery for everyday use.
- Using unique styles and techniques to convey narratives in ceramics.
Professional Accomplishments
- Showcased work in local and national art galleries, gaining recognition for craftsmanship.
- Received accolades for innovative designs in pottery competitions.