Embarking on the journey of how to glaze smoky qartaz pottery unveils a world where ceramics transcend mere function to become captivating artworks. The allure of smoky quartz glazes lies in their spellbinding depths and the play of shadow and light within their layered transparencies.
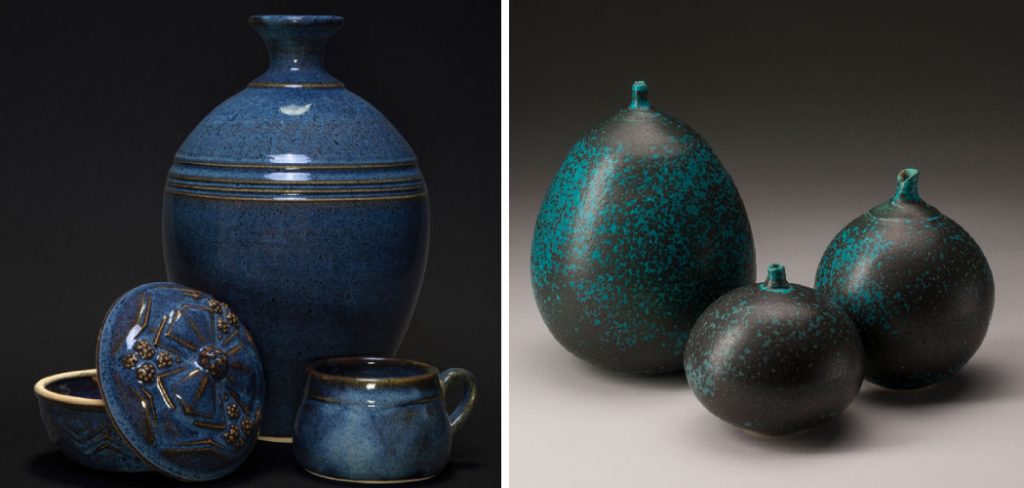
This guide aims to navigate potters through the mystical process of mastering these glazes, ushering them into an era of ceramic splendor rich with complexity and a smoldering, earthy palette. Join us as we explore the techniques and secrets to perfecting the smoky quartz finish, a testament to the craft’s profound beauty.
Understanding Smoky Quartz Glazes
A. Composition and Chemistry
Smoky quartz glazes are a ceramicist’s alchemy, turning ordinary vessels into treasures with their dusky luminescence. These glazes predominantly consist of silica, which forms the glassy matrix, and a combination of metal oxides like iron, manganese, and copper that provide the signature smoky color. Opacifiers such as tin oxide or zirconium may be added to adjust the translucency, allowing more or less of the clay body to show through.
The unique smoky effect arises from the light-scattering properties of these components and the interaction between the glaze and clay during the firing process. Artists can experiment with the material percentages to create an entire spectrum of finishes, from light wisps of smoke delicately veiling the piece to rich, deep charcoal hues that swallow the light and underscore textures.
B. Choosing the Right Smoky Quartz Glaze
Choosing a smoky quartz glaze must be carefully considered to ensure compatibility with the clay body and achieve the desired visual effect. Factors such as firing temperature play a vital role; high-fire glazes yield different textures and colors than low-fire glazes. The clay’s composition can also affect the glaze, influencing the final appearance. Resources such as The Ceramic Glaze Handbook by Mark Burleson or the Glazy.
org database provide extensive comparisons of glaze properties and firing outcomes for those seeking the perfect glaze. Additionally, pottery forums and community workshops offer invaluable insights from fellow potters’ hands-on experiences, making it easier to navigate the plethora of options and find a smoky quartz glaze that meets the potter’s artistic vision.
Preparing Your Canvas: Building the Foundation
A. Selecting the Ideal Clay Body
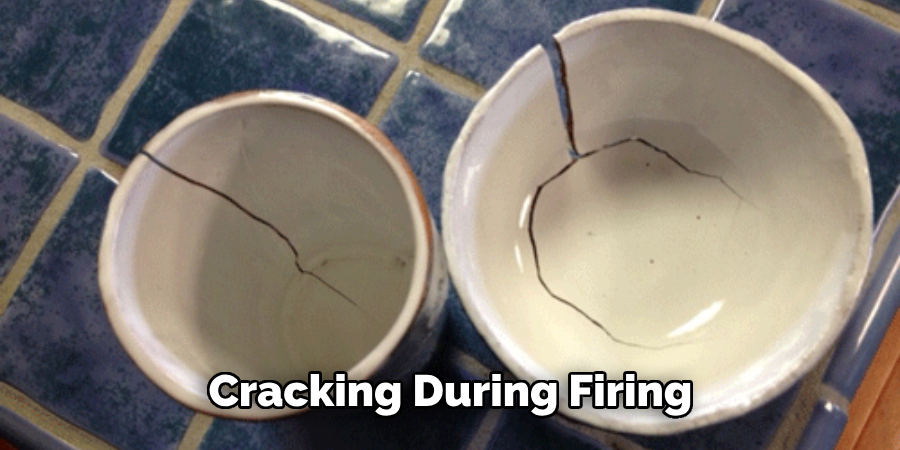
Choosing the correct clay body is crucial for smoky quartz glazes to unveil their full potential. Porcelain and white stoneware provide a light, uniform canvas that accentuates the glaze’s translucency and color depth. Additionally, these clays often accommodate a wide range of firing temperatures, making them versatile for various glaze recipes. One should be aware of the body’s shrinkage rate to avoid warping or cracking during firing. Opt for clays with low iron content to prevent unexpected color changes and ensure the glaze’s integrity.
B. Shaping Your Masterpiece
Crafting the form is the first act of bringing artistic vision to life. Techniques like hand-building, wheel throwing, and using molds each offer distinct advantages for shaping clay. For smoky quartz glazes, cleaning surfaces and eliminating imperfections are paramount. Meticulous smoothing ensures an even glaze coat without pinholes or sags. Whether pinching pots or centering on the wheel, the creator’s touch defines the final piece’s character, setting the stage for the glaze to enhance every curve and contour.
C. From Bisque to Canvas: Bisque Firing Essentials
Bisque firing transforms raw clay into a stable, porous state suited for glaze application. Successfully bisque wares provide a canvas that allows smoky quartz glazes to bond efficiently. Critical to this process is firing to the appropriate temperature, typically between Cone 08 and 04, securing the clay body’s maturity without over-vitrifying. A slow firing cycle is key to minimizing thermal shock and promoting even heat distribution, preventing defects like dunting. Ensure a consistent atmosphere in the kiln to avoid discrepancies in surface texture or glaze results post-firing.
How to Glaze Smoky Qartaz Pottery
1. Unveiling the Secrets of Depth and Mystery
A. Base Glazes: Setting the Stage
The foundational role of base glazes in smoky quartz pottery cannot be overstated, as they create the smooth canvas necessary for subsequent layers of decorative glaze to adhere and interact. A well-chosen base glaze should be sympathetic to the character of the smoky quartz effect, enhancing, rather than obscuring, its delicate hues.
Recognized options that pair well include transparent and semi-opaque base glazes, allowing the overlying colors to penetrate and merge. The application method—whether dipping for uniformity, pouring for gradient effects, or brushing for targeted areas—further manipulates the base to invite the mystical smoky essence.
B. Layering Magic: Building Smoky Dimensions
Embarking on the artful practice of layering glazes amplifies the smoky quartz appeal through depth and complexity. By meticulously superimposing different glazes, one captures variegated smoky tones, mirroring the amorphous nature of smoke itself. Key to this approach is the judicious use of translucent glazes, which, when layered atop one another, yield a range of intensities and shades—from faintly simmering undertones to deep, mesmerizing blacks.
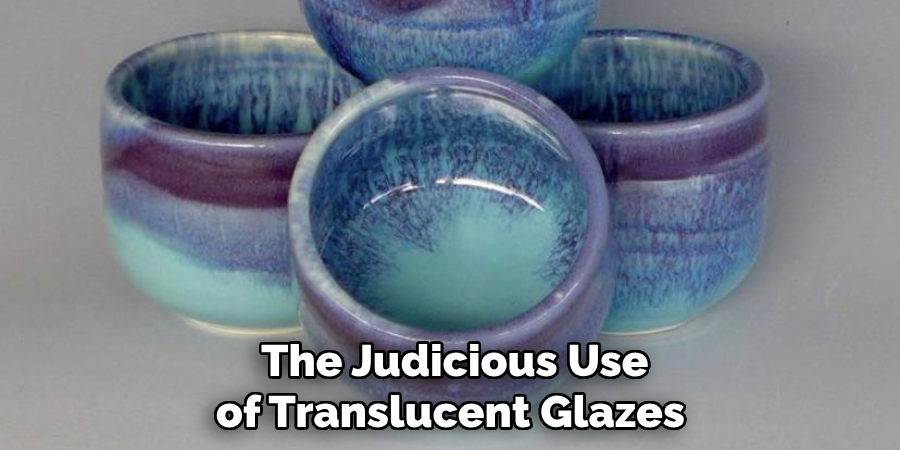
Precision in glaze viscosity and specific gravity is crucial, as these factors influence flow and interplay during firing. Artists often find success by pairing a stable base glaze with more fluid glazes to encourage movement and interactions that culminate in the smoky effect. Using calculated brushstrokes or utilizing resist methods, potters can control the ember-like burn of each layer, with areas of heavy application intensifying color and textural qualities. At the same time, lighter touches whisper of ephemeral smoke drifts, thereby achieving personalized artistic expressions and depth.
C. Accents and Highlights: Bringing Your Creation to Life
The deliberate application of glazing techniques to accentuate details imbues a piece with vitality and pronounced character. Utilize underglazes or stains to underscore handles, rims, or embossed textures—contrasting against the smoky quartz backdrop for a visual pop.
Whether wax-based or latex, resists are indispensable tools for safeguarding negative spaces or designing patterns that are untouched by smoke-infused glazes. The eye finds delightful resting places amidst the swirling, smoky aesthetic through this contrast. This intentionality in highlighting ensures that each feature partakes in the narrative, contributing to the pottery’s overall energy and dynamism.
D. Glazing for Texture: Embracing Roughness and Smoothness
The smoky quartz glaze interacts distinctively with textured surfaces, emphasizing grooves, valleys, carving, or impressions within the clay. These textures generate a captivating interplay of light and shadow, further pronounced by the glaze’s flow during the firing process.
Tactile surfaces require thoughtful glaze application; thick layers may fill in delicate textures, while sparse coats may not fully define the form’s physical nuances. It is a delicate balance wherein the potter must account for the glaze’s movement at high temperatures. Potential challenges include maintaining texture definition and preventing the glaze from pooling excessively, obscuring fine details.
2. Firing Your Masterpiece: Unveiling the Mystery
A. Choosing the Right Firing Schedule
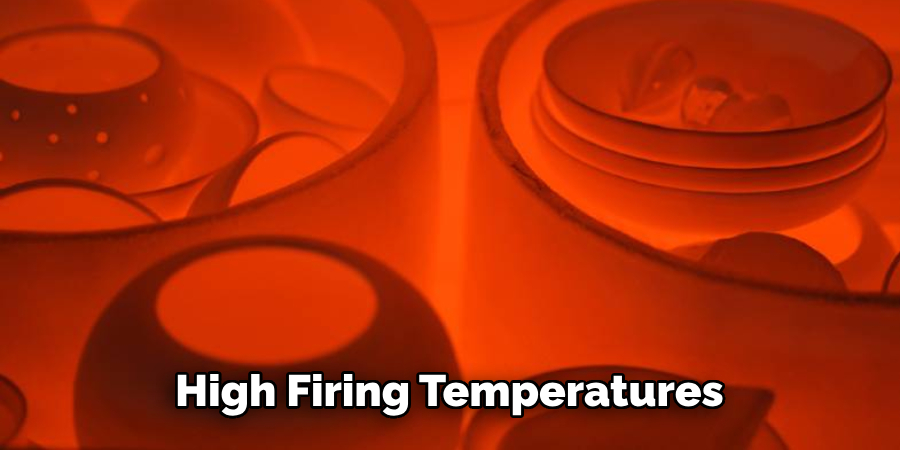
The journey of smoky quartz glazes culminates in the kiln, where firing schedules orchestrate the glaze’s transformation. The fate of these glazes hinges on both temperature and kiln atmosphere—oxidizing or reducing conditions can dramatically alter color and finish. High firing temperatures coax out depth and richness but demand tight control to prevent glaze run-off, while lower temperatures preserve subtle details and offer softer tones. Reduction firing can deepen color variations, adding an ethereal quality unique to smoky quartz effects.
Finding the right balance is key; thus, conducting test firings with meticulous notes can lead to selecting a firing schedule that marries an artist’s vision with the glaze’s inherent properties.
B. Cooling and Unveiling: The Moment of Truth
Once the peak temperature is reached, cooling becomes a critical phase. Rapid cooling may spawn hairline fractures or compromise glaze integrity, while a controlled cooldown allows for stabilization of the glaze, eliminating undesirable tension within the piece.
Patience during this stage is a virtue; the kiln’s slow revelation ensures the potter’s labor comes to fruition without thermal shock-induced heartbreak; as the temperature ebbs, anticipation mounts. At last, opening the kiln door unveils the product of creative alchemy: the depth, sheen, and mysteries of smoky quartz pottery emerge, ready to beguile the world with its gem-like splendor.
That’s it! You’ve now learned how to glaze smoky qartaz pottery, from selecting the right base glaze to firing and cooling your masterpiece. But don’t be afraid to experiment and put your own spin on these techniques. With practice and patience, you, too, can unleash the magic of depth and mystery in your pottery creations.
3. Beyond the Basics: Exploring Creative Frontiers
A. Experimenting with Multi-Firing Techniques
Adventurous potters may delve into multi-firing techniques to heighten the allure of their smoky quartz creations, embracing the chance to infuse their work with unprecedented beauty metrics. Luster firing involves a third firing process, adding metallic compounds to yield a shimmering surface—a striking complement to the glaze’s smoky depths. Likewise, smoke firing, traditionally done post-bisque firing, introduces carbon and smoke into the glaze, accentuating the quartz effect with haunting traces of organic patterns.
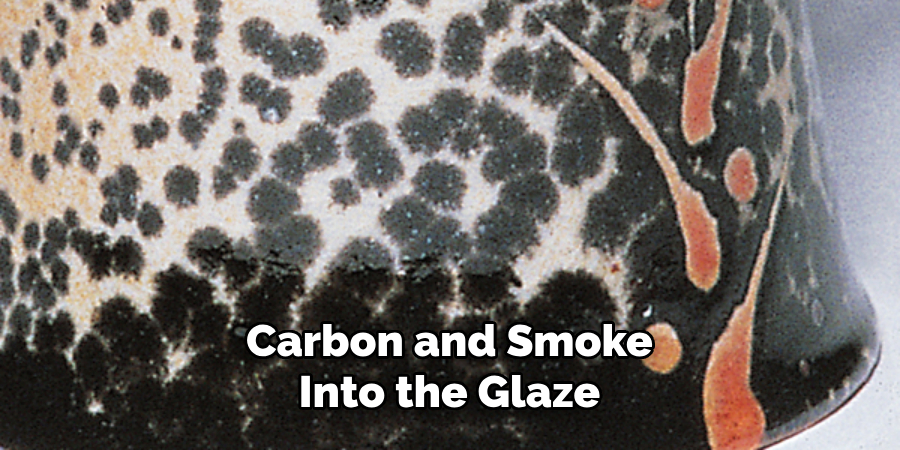
Raku, the dramatic Japanese technique, offers a color spectrum from metallic to crackled finishes, rebuking predictability with its unpredictable results. These techniques require careful planning—test pieces should precede full projects to gauge outcomes. Additionally, knowing each process’s unique temperature and atmospheric needs is indispensable for ensuring their successful integration with smoky quartz glazes.
B. Pushing Boundaries: Glazing with Other Techniques
The interplay of smoky quartz glazes with other glazing techniques can summon a symphony of texture, color, and depth, birthing masterpieces of intriguing complexity. Sgraffito, for instance, allows artists to ‘scratch away’ layers, revealing the contrastive underglazes beneath the quartz texture. Mishima, a slip-inlay technique, complements the smoky glaze by offering precision to designs, infusing it with clear, intricate imagery.
Cuerda Seca, with its defining technique of creating barriers for glazes, introduces unglazed regions that starkly contrast with the smoky fluidity. These combinations, however, come laced with challenges—each technique demands conscious application, meticulous timing, and an understanding of how they interact at varying temperatures.
Potters are encouraged to embrace these techniques as opportunities for growth, experimenting, and adjusting their fusion methods to produce distinct, memorable works that push the boundaries of ceramic artistry.
Troubleshooting: Navigating Challenges
A. Dealing with Unevenness: Achieving Consistency
Smoky quartz glazes often exhibit the challenge of unevenness—areas where glaze gathers more thickly or thinly, affecting the final appearance. To prevent this, potters should stir glazes thoroughly before use to ensure homogeneity. Applying consistent thickness glaze is crucial; dipping or spraying methods can help achieve a more uniform coat. Amendments to glaze recipes, such as adding flocculants or thickeners, might also improve application uniformity. Regularly calibrating application tools and techniques and maintaining diligent records will help refine processes for consistent glaze behavior.
B. Preventing Crawling: Solutions for a Smooth Finish
Crawling, where glaze retracts, leaving bare clay exposed, can mar the surface of smoky quartz pottery. A dusty bisque can cause this overly thick glaze application or insufficient clay-glaze interface. To avoid crawling, ensure bisque ware is clean and free of oils or dust before glazing. Consider slightly diluting glazes to promote better flow and adhesion and avoid over-applying. If problems persist, applying a holding spray or a thin slip between bisque and glaze may improve adhesion. Collaborating with fellow potters or online communities can provide additional insights and problem-solving techniques, bolstering the potter’s troubleshooting arsenal.
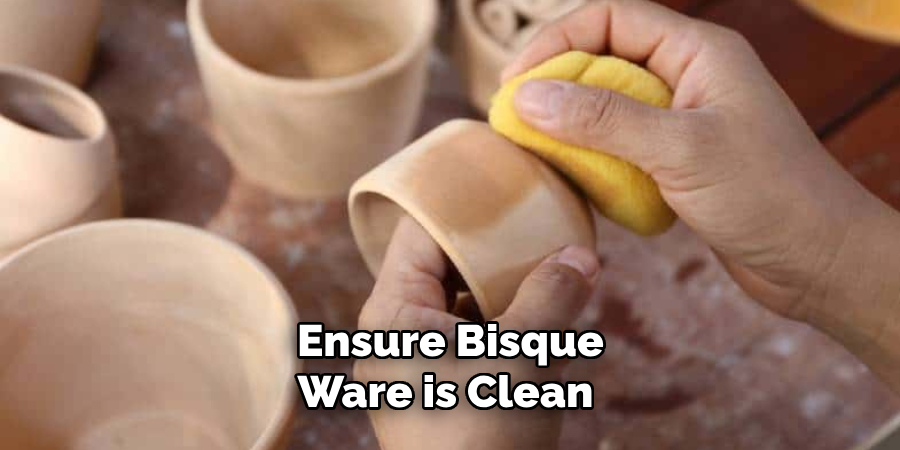
Inspiration Gallery: A Feast for the Eyes
Welcome to a visual symphony of smoky quartz pottery, where the melding of earth, fire, and artisan ingenuity illuminates the remarkable versatility of this glaze. Each piece showcased below is a testament to the artist’s dedication and an open invitation to explore smoky quartz’s endless creative potential.
- Ethereal Whorls Vase by Eleanor Gray: Expertly crafted with a reduction firing technique, this vase showcases dramatic swirls of deep garnet transitioning to a misty topaz, exemplifying the glaze’s mastery over gradient effects.
- Midnight Blossom Bowl by Shinzo Nakamura: Embracing Raku firing, Nakamura’s bowl captures the striking contrast between the silvery luster of metal inclusions and the glaze’s inherent shadowy tones, giving each blossom pattern a moonlit glow.
- Ancient Echoes Urn by Hafizah Binti Abdul: This stately urn demonstrates the power of smoke firing, with carbon trails etching organic stories into its surface, uniting millennia of traditions with modern craftsmanship.
- Celestial Carvings Plate by Maya Rossi: Rossi marries the sgraffito technique with smoky quartz glaze, meticulously carving celestial motifs that break through the dusk-like surface, creating a compelling dichotomy of light and dark.
Each piece not only reflects the boundless possibilities within smoky quartz glazing but also serves as a source of inspiration for both novice and seasoned potters alike.
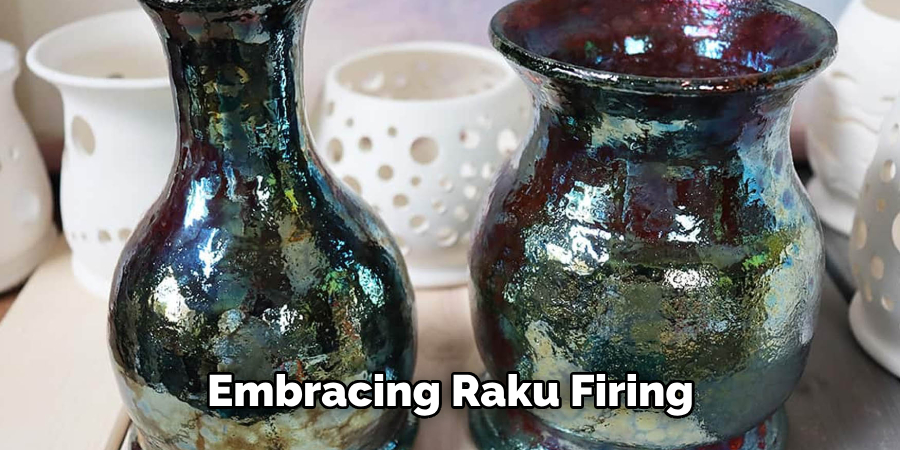
Mastering the Art: Tips from the Experts
Drawing from the wellsprings of seasoned mastery, here are invaluable insights from experts renowned for their smoky quartz creations. These snippets of wisdom aim to guide and inspire potters on their quest for glazing excellence.
- Giselle Huffman on Glaze Selection: “Choosing the right smoky quartz glaze is akin to selecting a fine wine—it must complement the form and spirit of your piece. I often start with a clear base and introduce my own blend of oxides for that personal touch.”
- Rajiv Anand on Application Techniques: “The application is all about control and knowing your tools. I prefer spraying for larger pieces to get that even coat and slow layering on smaller, intricate works.”
- Emilio Vasquez on Desired Effects: “Capture the essence of smoky quartz through trial and error; document each attempt meticulously. Subtle variations in temperature or reduction can yield profound differences. Always strive for balance in the unexpected.”
These experts underscore the need for experimentation, precise technique, and a reflective approach to perfecting smoky quartz glazing.
Frequently Asked Questions
Below is a compilation of frequently asked questions about smoky quartz glazing, designed to help potters navigate common curiosities and challenges:
Q1: Can Smoky Quartz Glazes Be Used in A Standard Electric Kiln?
A1: Yes, smoky quartz glazes can be fired in a standard electric kiln, though the results may differ from those achieved in reduction kilns. It’s important to follow the glaze manufacturer’s guidelines for the best results.
Q2: How Do I Fix Pinholes in My Smoky Quartz Glaze Application?
A2: Pinholes can be addressed by ensuring the glaze is sufficiently fluid, and the piece is thoroughly vented during firing. Sometimes, a second glaze application or firing can resolve pinholes.
Q3: Is It Possible to Achieve a Smoky Quartz Effect without High-Temperature Firing?
A3: While high-temperature firing typically enhances the depth of smoky quartz glazes, similar effects can sometimes be achieved at lower temperatures through glaze formulation and application techniques.
Q4: How Can I Prevent My Smoky Quartz Pieces from Sticking to The Kiln Shelf During Firing?
A4: To prevent sticking, it’s essential to use kiln wash on the shelves or to place the pieces on stilts or setters designed for high-temperature firing.
Q5: Can I Layer Smoky Quartz Glaze with Other Glazes for Different Effects?
A5: Absolutely. Layering smoky quartz glaze with other glazes can create unique effects. It’s important to test these combinations to ensure they are compatible and yield desirable results.
Q6: How Do I Control the Flow of The Glaze and Avoid Drips on My Pottery?
A6: To control glaze flow, apply the glaze in thin, even layers, and be mindful of the glaze’s viscosity. Adjustments can be made to the glaze recipe to affect how it flows during the firing.
Q7: What Safety Precautions Should I Take When Working with Smoky Quartz Glazes?
A7: Always wear protective gear such as masks and gloves when handling glaze materials, particularly in their powdered form. Work in a well-ventilated area to avoid inhaling any dust. Follow the safety guidelines provided with the glaze materials.
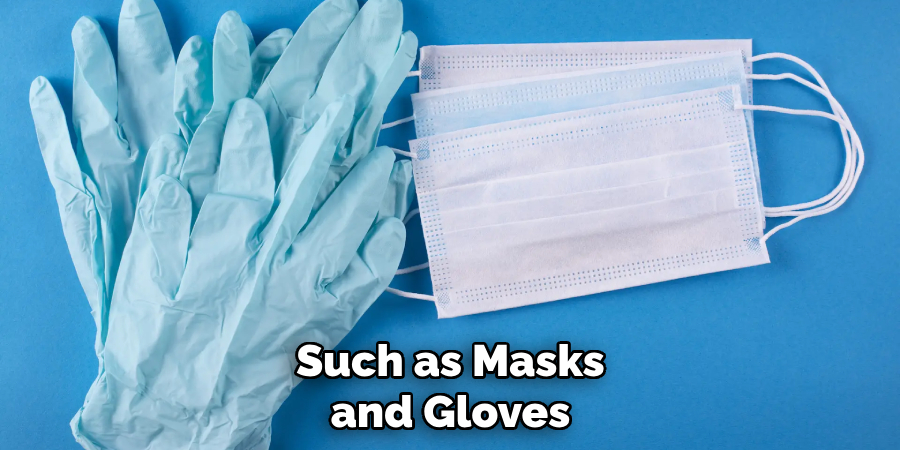
Conclusion
As we draw this guide to a close, it’s evident that understanding how to glaze smoky qartaz pottery is not only about the technical processes but also about the artistry it fosters within each creator. It is a journey of discovery, patience, and passion, revealing the distinct character of smoky quartz through every brush stroke and kiln firing.
Whether you are a novice potter or a seasoned artist, the adventure of mastering this elegant finish continues well beyond the confines of any studio. Embrace the challenges of learning how to glaze smoky quartz pottery, and let the vibrant community, diverse resources, and the fire of your creativity guide you. Ultimately, each piece—infused with your unique vision—becomes part of the shared tapestry of ceramic artistry that stretches across cultures and generations.
Toby Rede is a professional potter focused on creating functional and artistic ceramics. His work blends natural textures with modern forms, often inspired by sustainable gardening and outdoor environments. Toby’s pottery emphasizes both utility and beauty, reflecting his philosophy of intentional craftsmanship. On the blog, he shares insights on integrating handmade objects into everyday life.
Education
- Associate Degree in Ceramic Technology, Alfred University
Professional Focus
- Pottery creation with a focus on functionality and artistic expression
- Techniques exploring texture, glazing, and sustainable materials
Professional Accomplishments
- Work featured in regional art shows and garden exhibitions
- Collaborations with local craft fairs and home decor shops