Working with clay is both an art and a science. Whether you are a seasoned sculptor or a beginner, understanding how to achieve a smooth finish can significantly enhance your creations. A smooth surface not only provides an aesthetically pleasing appearance but also forms a better foundation for detailed finishing touches, such as painting or glazing. This guide will introduce you to essential techniques and tools, helping you master the art of smoothing out clay and elevating your pottery skills to the next level.
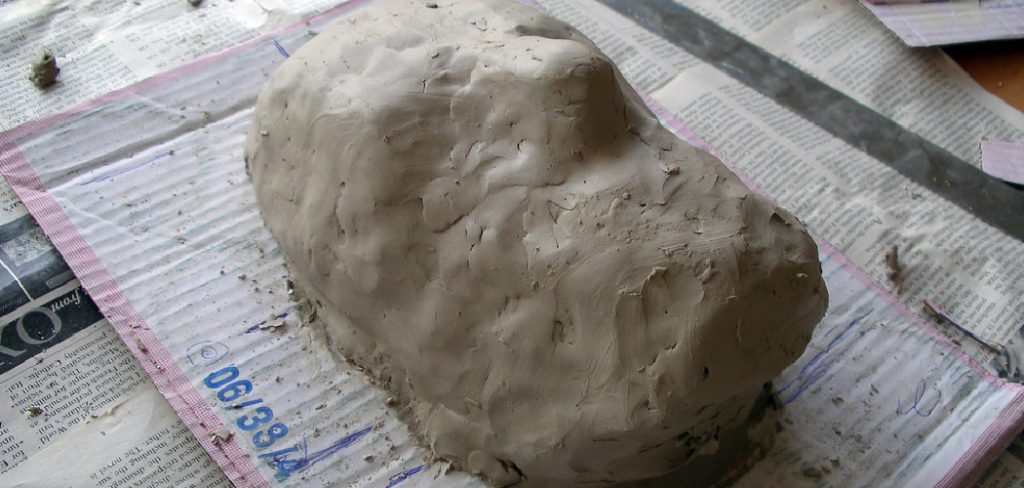
The Importance of Smooth Clay Surfaces
A smooth clay surface is essential for several reasons. It enhances the final product’s appearance, making your piece look professional and polished. A smooth finish provides an ideal base for decorations, glazes, or paints, bringing out the design elements in your work. Additionally, smoothing clay strengthens the piece by eliminating air pockets and inconsistencies, which helps prevent cracks and flaws during drying and firing. By mastering clay smoothing techniques, not only do you improve the aesthetic and functional quality of your creations, but you also expand your artistic possibilities.
Understanding Different Types of Clay
Clay comes in various types, each possessing unique characteristics that influence its behavior and suitability for specific projects. The three primary categories are earthenware, stoneware, and porcelain. Earthenware clays are typically red or brown and are known for their plasticity, making them ideal for beginners. They are fired at lower temperatures, resulting in a porous and less durable finish, which is perfect for decorative pieces. Stoneware clays, on the other hand, are more robust and fired at higher temperatures, making them suitable for functional ware such as utensils and dishes due to their durability and ability to hold glazes well. Porcelain clay, praised for its refined and translucent qualities, requires the highest firing temperatures.
It is favored by experienced potters for its delicate and sophisticated results, often used in fine art applications and luxury dinnerware. Understanding these types helps artists choose the right clay to match their vision and project requirements, ensuring a successful outcome.
Essential Tools for Smoothing Clay
Achieving a smooth clay surface requires precise tools that help potters refine their work with care. The rib is a fundamental tool, available in wood, rubber, or metal, each providing different flexibility and texture options. Natural sponges are key for gently smoothing surfaces while keeping the clay moist. Loop and ribbon tools are vital for trimming, removing excess clay, and smoothing tight or intricate areas. A metal scraper is excellent for shaving fine layers of clay to ensure an even finish.
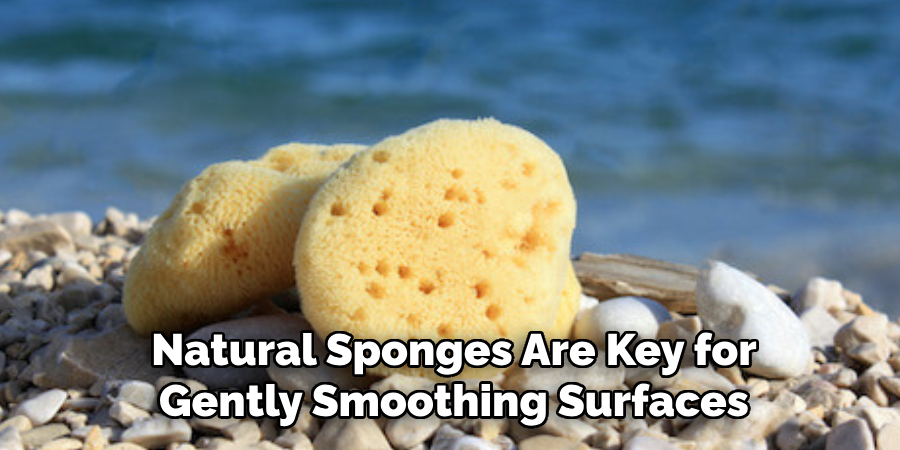
Finally, soft brushes and fingers often provide the finishing touch, leaving every surface polished. By integrating these essential tools into your pottery practice, you can control the texture and quality of your clay projects, achieving a professional and smooth finish.
10 Effective Methods How to Smooth Out Clay
Working with clay is a deeply satisfying and creative process, whether you’re a seasoned ceramicist or a beginner. However, achieving a smooth, flawless surface can often be challenging. In this listicle, we’ll explore ten effective methods that will help you smooth out your clay projects, ensuring your art is as polished as your vision.
1. Start with the Right Clay
Not all clays are created equal. Choosing the right type of clay for your project can significantly impact the finish. For example, porcelain clay is renowned for its smoothness, while stoneware may require more effort to achieve a polished look. Experiment with different types to find one that suits your needs.
2. Use a Rib Tool
A rib tool is essential for smoothing clay surfaces. Available in various materials, such as metal, wood, or rubber, rib tools help scrape and compress the clay, removing imperfections and creating a smooth finish. Opt for a flexible metal rib for best results when working with larger surfaces.
3. Utilize a Sponge
Sponges are versatile tools in the world of clay. A damp sponge can gently smooth the surface of your clay, eliminating any tool marks or small imperfections. Simply wipe the clay in a circular motion with a sponge to achieve a soft, even finish.
4. Try Sanding
Once your clay piece is dry, sanding can help achieve a smooth surface. Use fine-grit sandpaper and gently rub it over the clay in a circular motion. Be cautious not to sand too vigorously, as this can damage your piece. Sanding is particularly effective for hard clays or pieces with intricate details.
5. Experiment with Slip
Slip, a liquid mixture of clay and water, can be used to fill in small gaps and smooth out surfaces. Apply a thin layer of slip with a brush or your fingers, filling any imperfections. Allow it to dry, then gently smooth the surface with a sponge or rib tool.
6. Burnish with a Stone or Spoon
Burnishing involves rubbing the clay surface with a smooth, hard object like a spoon or stone. This technique compresses the clay particles and creates a polished, glossy finish. Burnishing works best on leather-hard clay and can add an elegant sheen to your work.
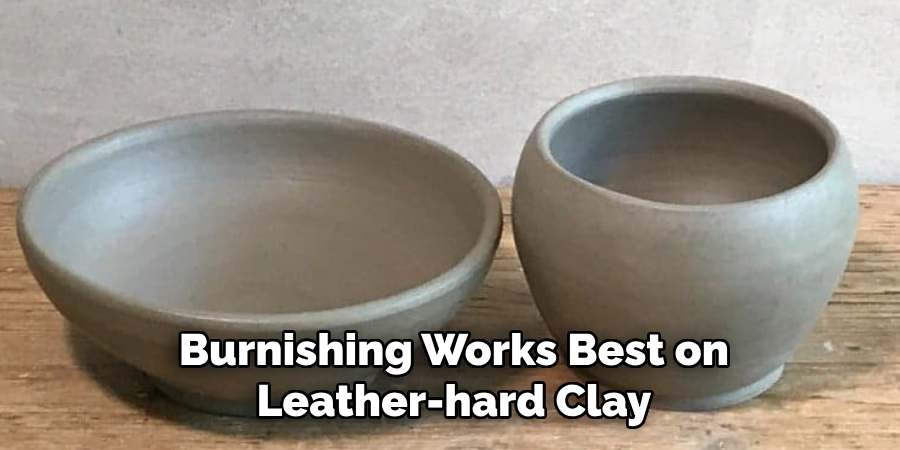
7. Use a Rubber Kidney
A rubber kidney is a soft, flexible tool perfect for smoothing and shaping clay. By gently running the rubber kidney over your piece, you can eliminate bumps and imperfections. This tool is particularly useful for refining curves and edges.
8. Apply a Thin Layer of Oil
For a final touch, lightly applying oil can add a smooth, glossy finish to your clay projects. Olive oil or baby oil works well. Simply apply a small amount to a soft cloth and gently rub it onto the clay’s surface. This method is best used on finished, fired pieces.
9. Dip in Glaze
Glazing not only adds color and protection to your clay but also helps smooth out surfaces. Applying a clear glaze over your piece can enhance its smoothness and shine. Remember to follow proper glazing techniques to achieve the best results.
10. Invest in a Polishing Wheel
If you’re serious about achieving a professional finish, consider investing in a polishing wheel. These tools provide consistent, high-speed rotations that can smooth and polish clay surfaces efficiently. They are particularly useful for larger clay pieces or high-frequency projects.
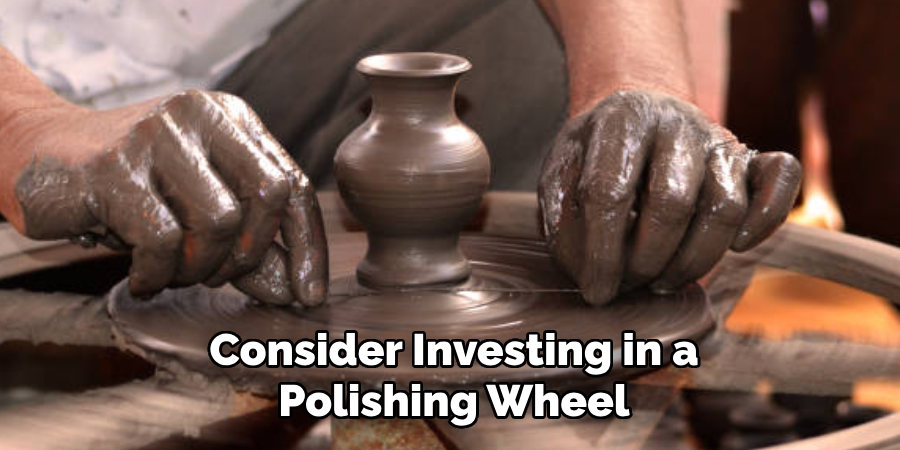
Maintenance and Upkeep of Clay Tools
Maintaining your clay tools is essential for ensuring their longevity and performance in future projects. Proper upkeep starts with cleaning tools immediately after use. Rinse any wet clay from tools under lukewarm water, making sure to remove all residue to prevent it from drying and hardening. When using metal tools, especially those prone to rust like metal ribs or loop tools, dry them thoroughly with a cloth post-cleaning. For wooden tools, occasional sanding can keep them smooth, while a light coat of mineral oil can help prevent cracking.
Rubber tools, such as rubber kidneys, should be stored away from direct sunlight to maintain their flexibility. Keeping your tools organized in a designated space ensures easy access and prevents damage. Regular maintenance not only preserves the quality of your tools but also contributes to the precision and professionalism of your clay work.
Troubleshooting Common Smoothing Issues
While striving for the perfect finish on your clay projects, you may encounter several common smoothing issues. Knowing how to troubleshoot these can help you achieve the results you desire.
Cracking Surfaces
Cracks often occur when your clay dries too quickly or unevenly. To address this, ensure your workspace is not too dry and consider covering your clay with plastic during breaks to maintain moisture levels. If cracks appear, you can fill them with slip and gently smooth them using a soft sponge or rib tool.
Residual Tool Marks
Tool marks can persist even after using smoothing tools. For fine marks, a damp sponge can work wonders by gently wiping the surface in a circular motion. Alternatively, try using a flexible rubber rib to compress the clay and eliminate marks.
Uneven Shading or Texture
If the surface of your clay shows uneven texture after smoothing, it may be due to inconsistent pressure or insufficient blending of slip. To remedy this, ensure even pressure distribution as you work, and consider reapplying slip, allowing it to dry before smoothing with a soft cloth or sponge.
Over-sanding Damage
Over-sanding can damage the integrity of your piece, leading to unwanted thin spots or rough patches. To prevent this, always use fine-grit sandpaper and apply light, circular strokes. If damage occurs, you may need to reinforce the area with additional clay and re-smooth.
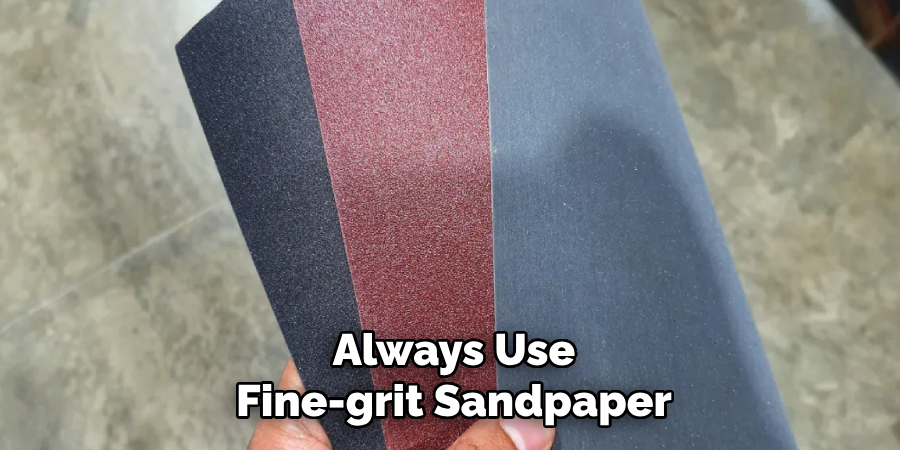
Difficulty with Burnishing
Achieving the perfect sheen from burnishing may require practice. Ensure your clay is at the right leather-hard stage before beginning, and use a smooth, hard object like a spoon for consistent results. If results are still lackluster, consider refining your technique with additional practice to achieve that polished glow.
Conclusion
Smoothing clay is a crucial skill for every ceramics enthusiast, whether you’re just starting or have years of experience. We’ve covered a range of techniques in this guide, from basic tools like sponges and sandpaper to advanced methods such as burnishing and glazing. Each technique offers a unique way to improve the quality and appearance of your clay creations.
Toby Rede is a professional potter focused on creating functional and artistic ceramics. His work blends natural textures with modern forms, often inspired by sustainable gardening and outdoor environments. Toby’s pottery emphasizes both utility and beauty, reflecting his philosophy of intentional craftsmanship. On the blog, he shares insights on integrating handmade objects into everyday life.
Education
- Associate Degree in Ceramic Technology, Alfred University
Professional Focus
- Pottery creation with a focus on functionality and artistic expression
- Techniques exploring texture, glazing, and sustainable materials
Professional Accomplishments
- Work featured in regional art shows and garden exhibitions
- Collaborations with local craft fairs and home decor shops